NMFE Plating Barrel Advantage
Think all plating barrels are made the same? Think again. Our industry experience over the past two decades led to strategic design choices that make the Novo Metal Finishing Equipment plating barrels stand out. Our barrels are engineered to improve process efficiency, increase barrel durability and maintain chemical resistance over the lifetime of the barrel.
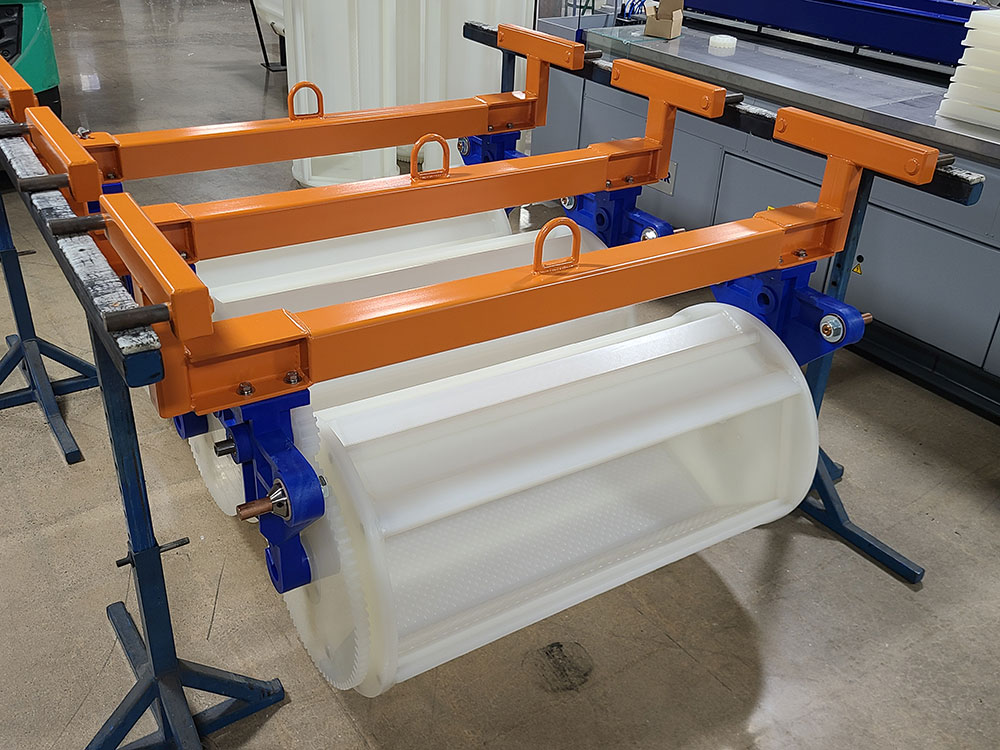
We are Novo Metal Finishing Equipment (Novo MFE), a domestic designer, fabricator and assembler of best-in-class plating equipment for the metal finishing industry. Founded in 2001 as Core Plating Technology, Novo MFE was purchased by local industrial manufacturing company Novo Precision in 2021. We operate a complete manufacturing facility within the Novo Campus in Bristol, Connecticut.
Below, we’ll explain what makes our US-engineered and manufactured plating barrels stand out.
Process Efficiency
We’ve incorporated best practices that we’ve learned over years into our barrel design in order to increase solution flow and reduce fluid dragout (drag-out). Every design and process detail of the Novo Metal Finishing Equipment barrel ties back to improving fluid flow.
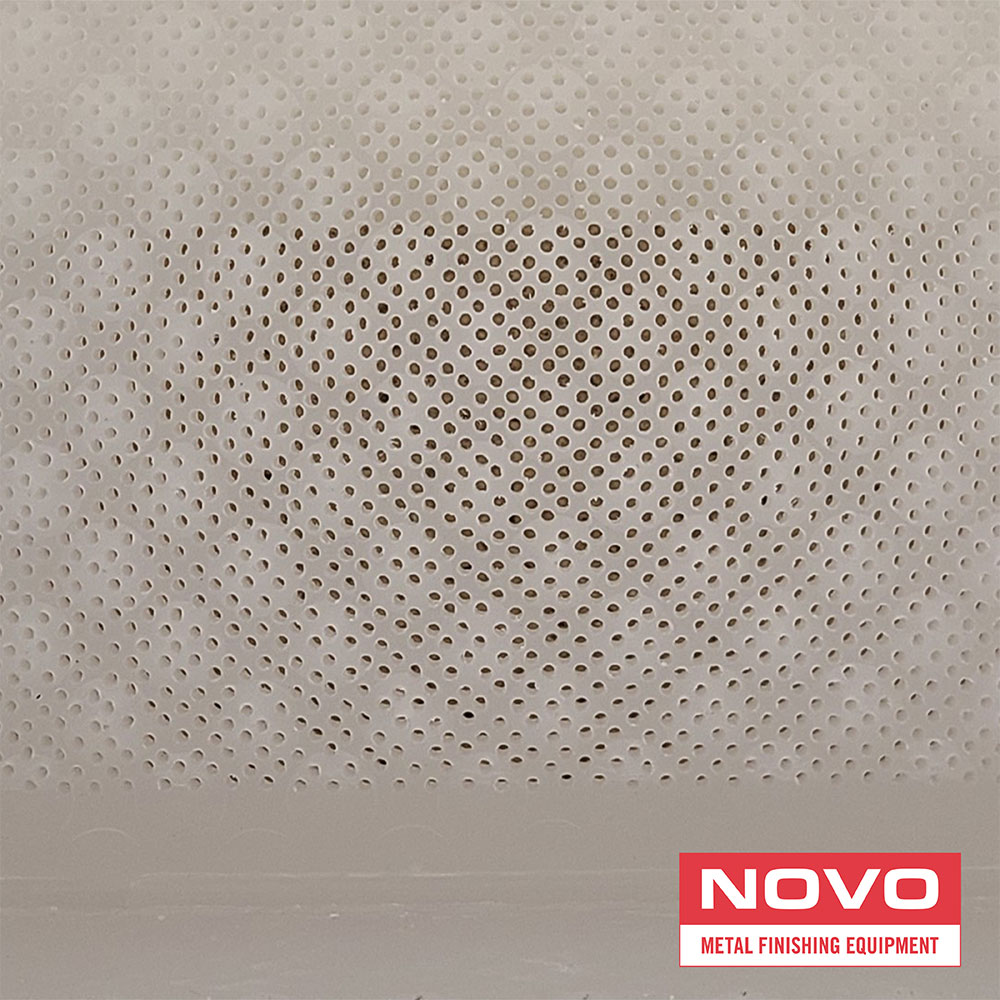
Our barrels are constructed using a single, molded body. By thermally bending the body instead of hand welding pieces together, we create an even surface where flat edges come together that is significantly less susceptible to trapping fluid or cracking over time. We also use a tight drill pattern along the body of the barrel, which it provides excellent solution flow and drainage. We know that the better the solution exchange, the less time parts need in the tank.
In addition to fluid flow, our plating barrels have several design elements that prevent parts from getting trapped or stuck in the barrel. First, we use Proteus® PP, ProKnob Polypropylene textured panels that do not allow flat, thin or light parts to adhere to the sides of the barrel. Second, we use a robust box-style door with additional bracing around the edges of the door. This reinforced door design maintains the structural integrity of the door over time and prevents door warping. Warped doors allow flat and small parts to become trapped in the gaps over time which then accelerates door warping. Together, all of these design elements encourage solution exchange, parts turnover and uniform part coating.
Long Term Barrel Durability
The Novo Metal Finishing Equipment barrel is designed for load durability.
The body of the barrel is extrusion welded to the base, which creates a higher integrity joint when compared to hand welded joints. Traditionally, plating barrels are under supported, leaving them susceptible to warping and breaking over time. Our barrels have several vertical back braces in anticipation of repetitive use and abuse. The Novo MFE barrels are also designed with butt welded door frames, which strengthen the door side of the barrel without creating another trap for fluid or parts. Finally, the robust custom pull gear is securely mounted on the barrel and can be replaced (if ever necessary), in the field. We machine pull gears at our facility to our customer’s specification including thickness, number of teeth and pitch.
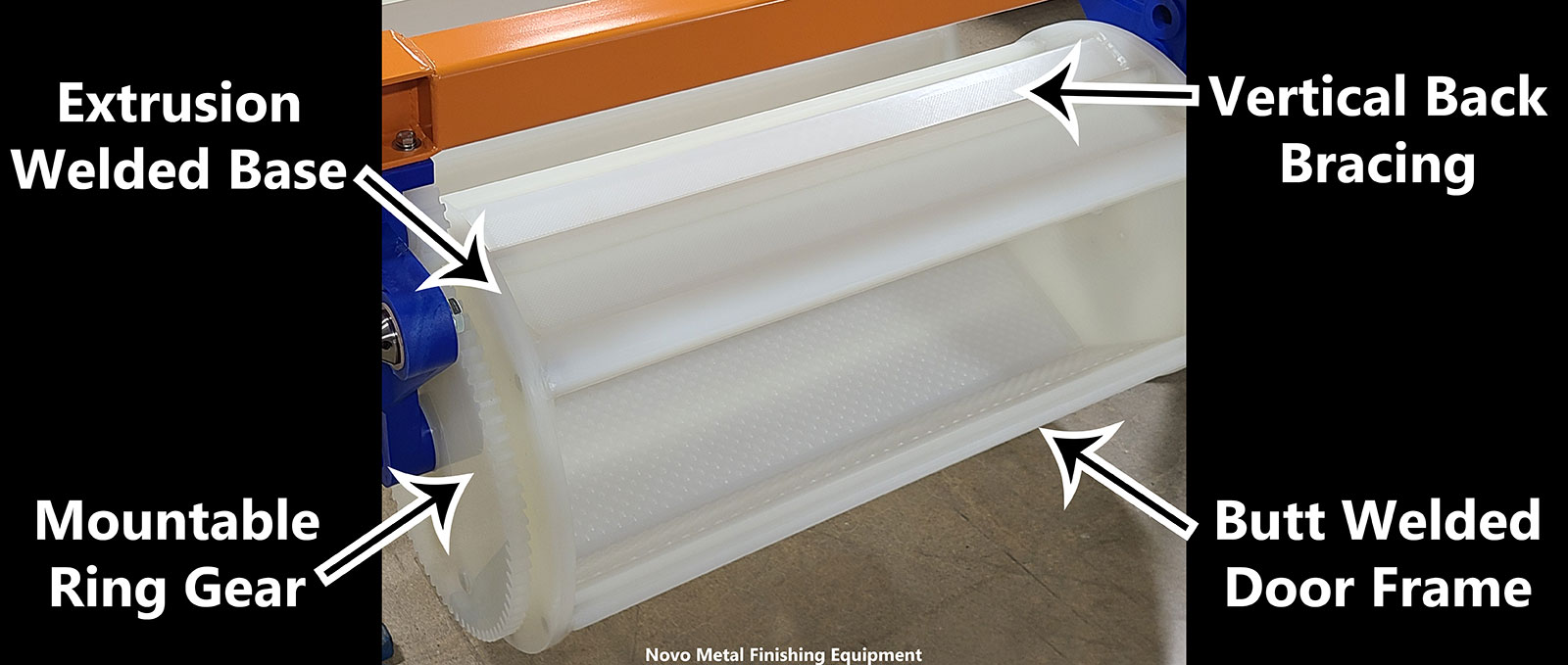
Material Durability
In the plating and surface finishing industries, chemical resistance is table stakes. However, our design team incorporated a few details that improve the lifespan of our barrel. Our plating barrels are made from polypropylene for maximum moisture and chemical resistance. The tight drill pattern and molded body improves fluid flow and reduces possibility of long-term exposure due to trapped chemicals. Not all customers are processing similar parts. Through experience, we know how to design a barrel (and electrode) for challenging parts such as chains and long screws. Since we also provide all of the replacement parts including gears, saddles, horns, hanger arms and danglers, we can create a customized part package that fits the exact need of each of our customers.
Here at Novo Metal Finishing Equipment, we’ve worked in the surface finishing and plating industry for over 20 years. We are a designer, fabricator and assembler of best-in-class plating equipment for the metal finishing industry. We operate a complete manufacturing facility within the Novo Campus in Bristol, Connecticut. Our barrels are engineered to improve process efficiency, increase barrel durability and maintain chemical resistance over the lifetime of the barrel. Novo Metal Finishing Equipment’s catalog of replacement components includes tanks, plating barrels, barrel hanger arms, rack saddles and horns, portable barrels, plating lines, gears, dangler assemblies and other plating line components.
For more information on what we can do for you, get in touch with us.